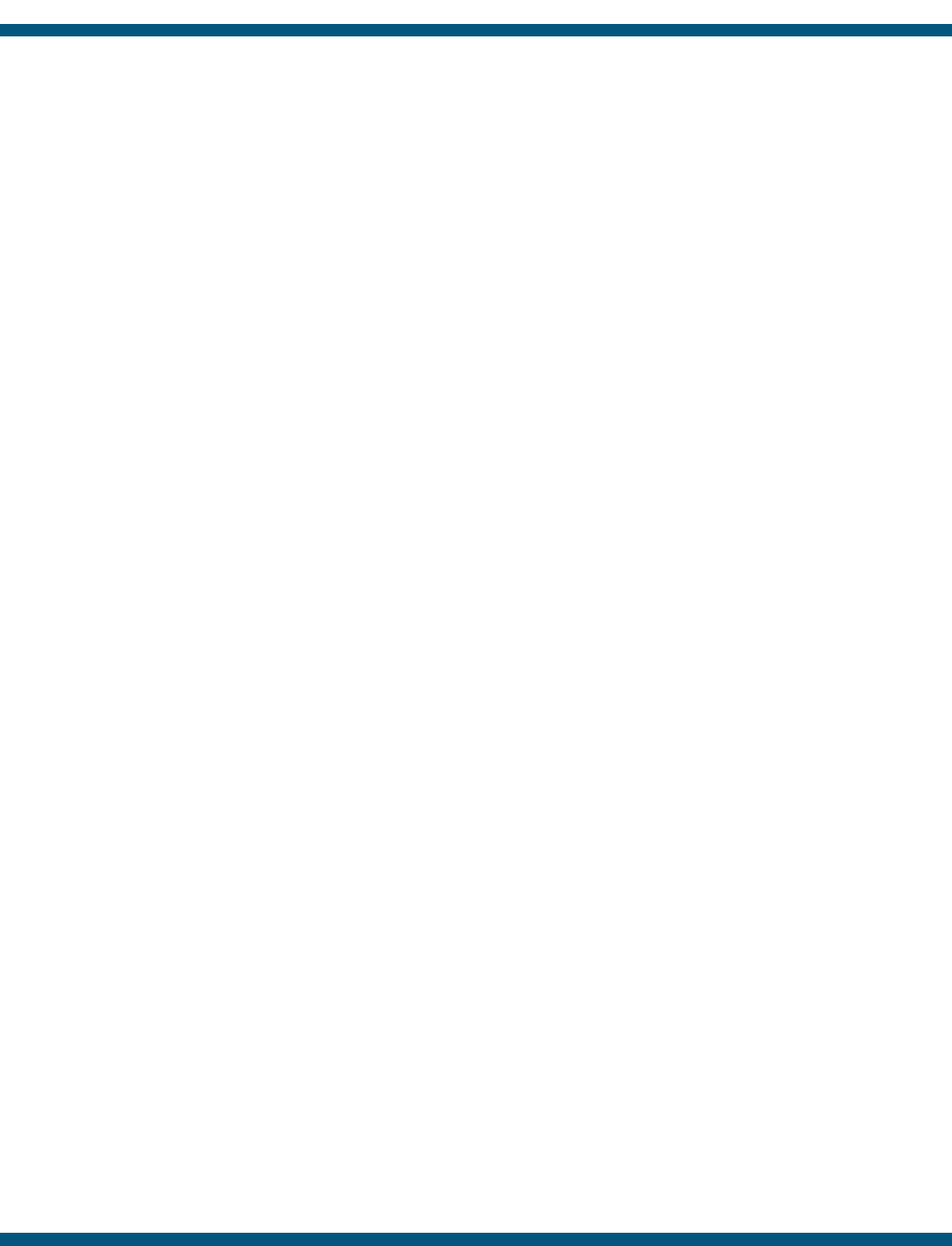
References
Aspen Publishers2000.“HowAttachedGaragesPoisonOurIndoorAir,AndWhatBuildersCanDoAboutIt.”inEnergy Design Update,Volume20,
No.12;December2000http://arkansasenergy.org/business_development/energy/les/Clearinghouse/How%20Attached%20Garages%20Poison%20
Our%20Indoor%20Air.pdf
ASTM1991.“StandardTestMethodforDeterminingtheRateofAirLeakagethroughExteriorWindows,CurtainWalls,andDoorsunderSpecied
PressureDierencesacrosstheSpecimen.”ASTME283-91,WestConshohocken,Pennsylvania.
Building America Best Practices, Volumes 1–9. TheseBestPracticesGuidesfromtheU.S.DepartmentofEnergyprovidebuildingscienceguidance
forbuildersofenergyecienthomesineveryU.S.climatezone.Availableforfreedownloadat
http://www1.eere.energy.gov/buildings/building_america/publications.html
Braun, B. J. Hansen, and T. Woods1995.“Urethanefoamsandairleakagecontrol”Home EnergyVol.12(4),publishedJul-Aug1995.
Brown, Evan1999.Energy Performance Evaluation of New Homes in Arkansas,EvanBrown,consultanttotheArkansasEnergyOce,December1999,
www.energycodes.gov/implement/pdfs/Arkansas_rpt.pdf
Building Science Corporation2006.Read This Before You Design, Build, or Renovate
www.buildingscience.com/documents/primers/plonearticlemultipage.2006-12-05.5229931729/section-2-recommendations
Building Science Corporation2009a.“AirBarriers—Tub,ShowerandFireplaceEnclosures,”InformationSheet407forAllClimates5/20/2009,
preparedbyBSCforDOE’sBuildingAmericaprogram,www.buildingscience.com/documents/information-sheets/4-air-barriers/air-barriers2014tub-
shower-and-replace-enclosures/?searchterm=building%20america
Building Science Corporation2009b.“AirSealingWindows,”InformationSheet406forAllClimates5/20/2009,preparedbyBSCforDOE’sBuildingAmerica
program, www.buildingscience.com/documents/information-sheets/4-air-barriers/sealing-air-barrier-penetrations/?searchterm=building%20america
Building Science Corporation2009c.“CriticalSeal(SprayFoamatRimJoist)”InformationSheet408forAllClimates09/18/2009,preparedbyBSC
forDOE’sBuildingAmericaprogram,www.buildingscience.com/documents/information-sheets/4-air-barriers/info-408-critical-seal-spray-foam-at-
rim-joist/?searchterm=building%20america
Building Science Corporation2009d.Duct Sealing,InformationSheet603,preparedbyBSCforDOE’sBuildingAmericaprogram.
www.buildingscience.com/documents/information-sheets/hvac-plumbing-and-electrical/information-sheet-duct-sealing/?searchterm=building%20america
Building Science Corporation 2009e.“SealingAirBarrierPenetrations,”InformationSheet405forAllClimates5/20/2009,preparedby
BSCforDOE’sBuildingAmericaprogram,www.buildingscience.com/documents/information-sheets/4-air-barriers/sealing-air-barrier-
penetrations/?searchterm=building%20america
Conbere, Susan and Kate Fried2006.“ADoctorintheHouse;BuildingperformancetestinghasgivenoneIllinoisremodeleranedgeinhis
market-andonthebooks,”Professional Remodeler,June1,2006.
Consumer Product Safety Commission2010.“WhatYouShouldKnowAboutCombustionAppliancesandIndoorAirPollution.”CPSCDocument#452,
accessed3/12/2010,www.cpsc.gov/cpscpub/pubs/452.html
Cummings, J.B., J.J. Tooley, N. Moyer, and R. Dunsmore, “Impacts of duct leakage on infiltration rates, space conditioning energy use, and peak
electricaldemandinFloridahomes,”inProceedings of the 1990 ACEEE Summer Study on Energy Eciency in Buildings,Asilomar,CA,(1990),pp.69–76.
Dalicieux P and C Nicolas 1990.“VentilationPerturbationsDuetoanOpenFireplaceinaHouse.”Energy and Buildings14(3):211-214
Davis2001.Whole House Fan Installation,BuildingDepartment,CityofDavis,California,July23,2001.www.city.davis.ca.us/cdd/pdfs/Whole_House_Fan.pdf
Granade, HC, J Creyts, A Derkach, P Farese, S Nyquist, and K Ostrowski2009.Unlocking Energy Eciency in the US Economy.
McKinseyandCompany.www.mckinsey.com/clientservice/electricpowernaturalgas/US_energy_eciency/
House Energy2009.“VentilationandElectricalPenetrations,”webpage,www.house-energy.com/AirLeaking/HvacAL.html
Iowa Energy Center 2008.Home Tightening, Insulation, and Ventilation,HomeSeries1,IowaEnergyCenter,Ames,Iowa.
www.energy.iastate.edu/homeseries/downloads/HomeSeries1.pdf
2009 International Residential Code For One- and Two-Family Dwellings. www.iccsafe.org
Jump, D. and M. Modera1994.Energy Impacts of Attic Duct Retrofits in Sacramento Houses,LBL-35375,preparedbyLawrenceBerkeleyNational
Laboratory,fortheU.S.DepartmentofEnergy,Washington,DC.
Karins, N.H., A. Tuluca, and M. Modera1997.Eectiveness of Duct Sealing and Duct Insulation in Multi-Family Buildings.
PreparedbyStevenWinterAssociatesandLawrenceBerkeleyNationalLaboratoryfortheNewYorkStateEnergyResearchandDevelopment
Authority and the U.S. Department of Energy.
Lstiburek, Joseph 2004a.Builders Guides.Guidestomixedhumid,hot-dry,mixed-dry,andcoldclimates,forpurchaseatwww.eeba.org/bookstore.
Lstiburek, Joseph W.2004b.Conditioned Crawl Space Construction, Performance and Codes,ResearchReport–0401,BuildingScienceCorporation,
www.building science.com